労働力不足への対策
2011年を境に日本の人口は減少に転じており、高齢化の進展に加えて世帯構造(共働きや単身の増加)が変わってきています。数年来続いている物流業界の労働力不足は賃金高騰にも表れており、物流業の平均時給は2017年10月までに68か月連続でアップしています。この傾向は引き続き継続するものとみられ、根本的な解決策が必要となっています。
雇い入れる賃金を上げても物流業界に労働者が集まらない状況の中で、解決策の一つが省人化・省力化・効率化ですが、日本政府は本格的にその方向性を打ち出しました。2017年7月28日に閣議決定された、「総合物流施策大綱(2017年度~2020年度)について」の内容において、労働力不足への対応について以下の2点が述べられています。
- 新技術(IoT、BD、AI 等)の活用による“物流革命(=革命的に変化する)”
- 人材の確保・育成、物流への理解を深めるための国民への啓発活動等
新技術については、トラックの隊列走行や自動運転化、ドローン配送、船舶の自動運航化・遠隔集中監視、物流センターでの自動化・機械化等を進めると謳われており、人材の確保・育成では、引き続き現場で必要とされる技能等の習熟のための検定や、物流の適切な管理に資する民間資格等の活用が必要であると謳われています。自動化と人材確保の両面で進めていくということです。
ロボット技術の導入と自動認識技術
これまでの物流分野における自動化技術の導入は、主に資本効率向上や生産性効果を期待してのものでしたが、今後は労働力不足への対応手段が主な目的となります。マテハンメーカーにとって物流事業者および製造業の物流分野は主要ターゲットですが、最近よく見られる取り組みとしては、ロボット技術の取り組みによるハンドリングの無人化・高機能化などがあげられます。
これまで産業用ロボットは製造現場である工場で利用されることが多かったのですが、物流分野への適用は、以下の2点がハードルとして考えられます。
(1)製造元が異なる不特定のモノを取り扱いできるのか
(2)設計情報が不明なものを取り扱いできるのか
ロボットによるモノのハンドリングの際には、SKU(Stock Keeping Unit):最小管理単位の情報が必要です。情報がマスター化されている製造現場であればロボットでのオペレーションが可能ですが、情報が乏しい物流センターでは困難になります。しかもハンドリングで必要なマスター情報は、縦・横・高さの形状だけではなく、色、硬さ、重心位置なども必要となる場合があります。ピッキング時やパレタイズ時に硬さが分からず、「ロボットアームで掴んだ時にモノを潰してしまった」、「重心位置が分からず持ち上げた時にモノを落としてしまった」ということが起こりかねません。
モノの情報をどのように得るのかが、物流現場で産業用ロボットに仕事をさせるために重要となります。その方法は大きく以下の2パターンに分かれます。
(1)製品マスター情報(形状、硬さ、重心など)を製造現場でICチップに書き込み、それを物流現場で読み取ってロボットに作業をさせる方法
(2)物流現場でハンドリング対象のモノを複数台の3Dカメラやレーザーで捉え、特異点情報を取得してピッキング作業などのハンドリングを行う方法
ICチップに書き込む方法をとる場合、サプライチェーンのどこの段階でICチップを貼付するのかは、RFIDによる自動認識技術の導入の際に議論になるところです。物流はサプライチェーンのキープレイヤーですが、製造業やそのサプライヤーにICチップ活用によるコストダウンを提案しても、そのコストダウンの範囲が物流に留まるのであれば、受入れが難しいというのが現実です。
物流分野の省人化・省力化・効率化を実施するためには、物流分野自体にて自動認識技術の導入を検討すべきだと考えています。
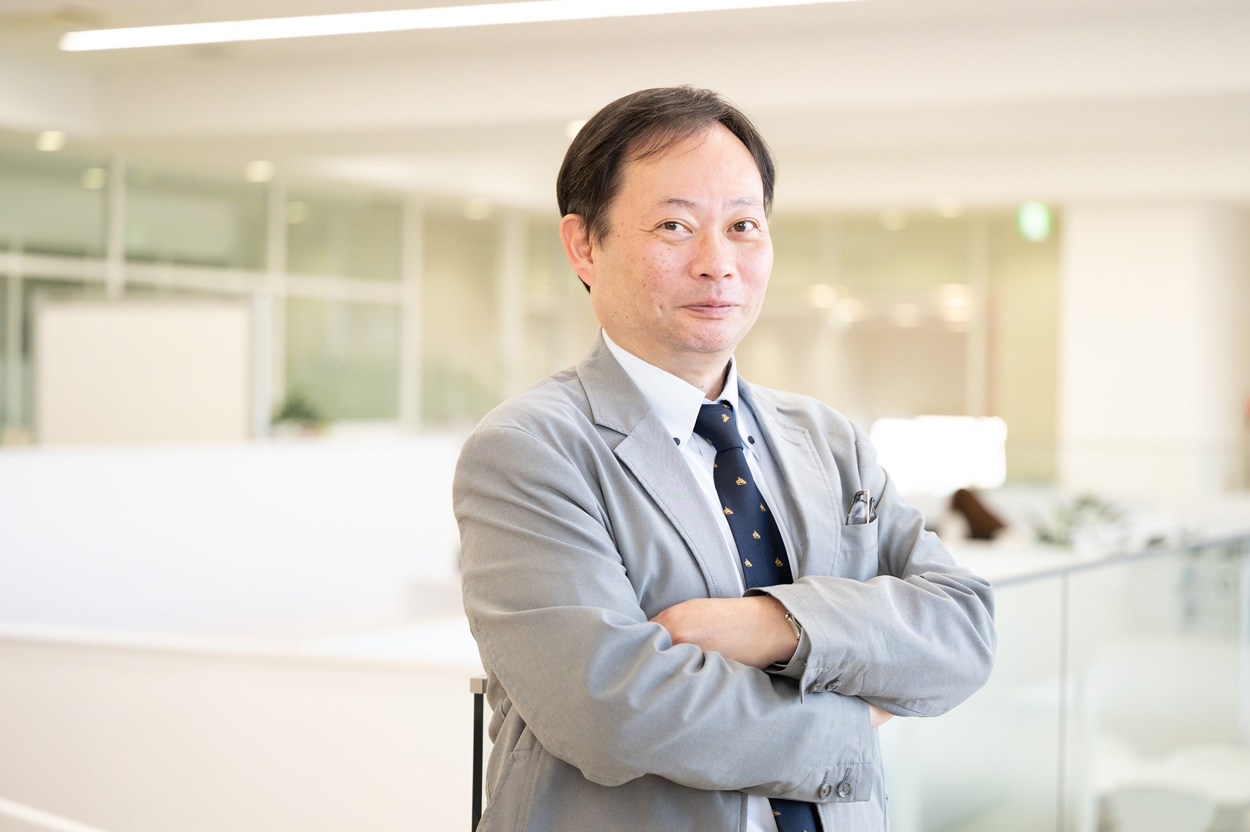
(文責:釜屋 大和)
ロジ・ソリューションでは、物流に関するいろいろなご支援をさせていただいております。何かお困りのことがありましたらぜひお声掛けください。(お問い合せはこちら)
━━━━━━━━━━━━━━━━━━━━━━━━━━━━━━━
★掲載された記事の内容を許可なく転載することはご遠慮ください。
(ロジ・ソリューション(株) メールマガジン/ばんばん通信第373号 2017年12月27日)
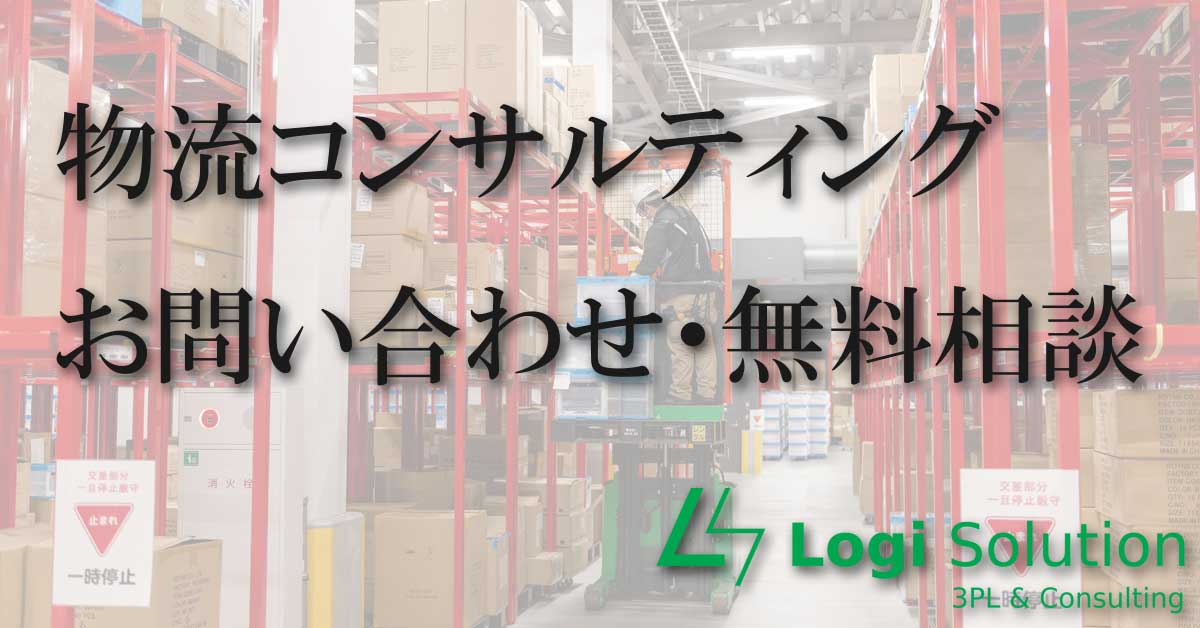